Contamination Control is a Critical Area in the assurance of the achievement in the appropriate product to meet the expected quality in Electronic Industry. A well designed Contamination Control System or Scavenging Vacuum System as it normally called is the first step towards the achievement of the appropriate production yield.
The less time your employees spend cleaning up dust or dirt, the more time they can spend productively operating in the production line. Contaminating Particles from production process such as lead oxides, berylium, arsenic, etc is taken out of the air before they can inhaled or contaminate the Clean Production Environment especially in Clean Room Production.
In fact, most advanced Clean Room Production
Machine nowadays, incorporate Scavenging
Capabilities within their machine to allow
a Central Scavenging Vacuum System to
be connected easily to it. Contaminating
Particles generated during the production
process is removed instantaneously instead
of leaving it to pollute the Clean Indoor
Climate affecting production yield and
reducing the need for any extra cleaning
activities.
In this way, even the smallest micro dust is removed without any posssibility of contaminating the production process.
So what is a Scavenging Vacuum System?
The Old way to handle the dust or
contaminated particle with a laminar flow
or low vacuum / high volume collection
system just does not work anymore. The
size of allowable contaminating particles
within a clean room area or regulations
established to protect the workers' health
just make such an option obsolete.
Scavenging Vacuum System which uses high
vacuum / high velocity / low volume air
flow to take away almost instantaneously
within inches where any contaminating
particles are generated is taking centerstage
The Centrally Located Vacuum Source is
connected by a network of pipes to inlets
which is conveniently located throughout
the production area to serve the production
machinery or any particular source of
contaminating particles. Such particles
are removed within inches of where they
are generated via small flexible tubes
or collection shrouds connected to each
production machine.
|
The information which we require to make an offer: |
|
|
> |
The Type of Dust or Process which will be hook up to the system. |
|
|
> |
The Vacuum Requirement of Individual Production Machines. |
|
|
> |
The Layout of the Plant and the Perferred Location of the Central Plant. |
|
|
> |
Any specific Preference of the client. |
|
|
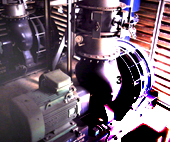 |
|
2 x 132 Kw Scavenging Vacuum Exhauster Installed at Seagate Media in Tuas - Singapore |
|
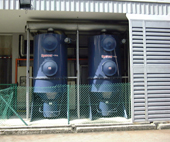 |
|
3000 SCFM Rate Vacuum Separator Installed at Seagate Media in Tuas - Singapore |
|
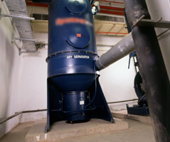 |
|
4100 SCFM Rated Vacuum Separator Installed in Seagate Media Facility in Gambas - Singapore |
|
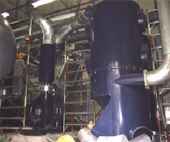 |
|
2 x 200 HP Scavenging Vacuum Exhauster installed for Media Production Facility |
|
|